Empowering Customers with Digital Integration
Date: 22/07/2021
As lockdown is easing, trade is swelling and customers are keen to fulfil their pent-up demand and make up for lost shopping time. Satisfying their ever-growing appetite for speedy delivery is proving a considerable task for Britain’s biggest retail supply chains.
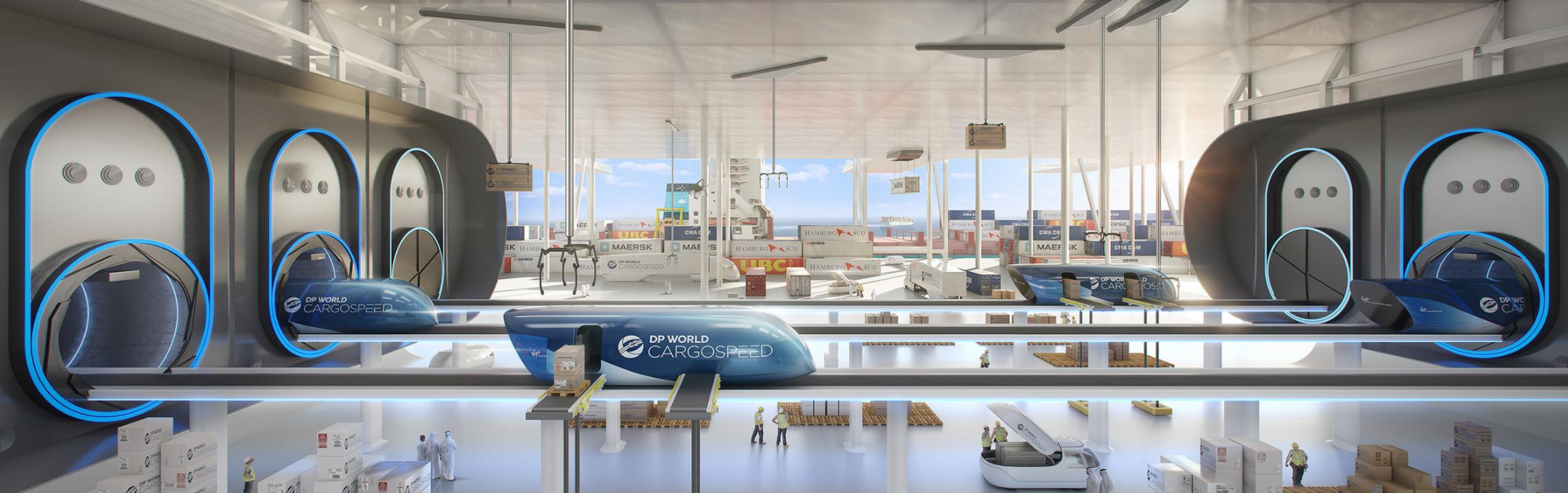
Retailers who have best managed this challenge throughout the pandemic include Morrisons and Card Factory. The efficient, resilient and predictable supply chains they’ve built are the result of solid investment in vertically integrated logistics. With the increased oversight this investment has provided, they’ve been able to use real-time data capture to keep their customers happy.
Digital solutions are providing the oversight supply chains have long needed. Everyone from shipping lines, cargo owners and end customers deserve real-time transparency on how and where their products are moving.
At DP World in the UK, digital solutions are something we’re integrating into the very infrastructure of our ports.
At DP World Southampton, our quayside teams are using Panasonic Toughbooks to transform productivity and customer service. These industrial tablets are equipped with mobile computing software that tracks each container, ensuring the safe and correct loading and discharging of goods on each vessel visiting the terminal.
Since the introduction of the Panasonic Toughbooks at Southampton, the quay crane move rate has increased, meaning ships have shorter stays and can travel to their next port sooner. Live updates from the devices are passed through to the customer via the DP World “Where’s My Container?” website.
“No other terminal uses a mobile device with software as advanced that enables an operator to interact with the loading and discharging of a vessel in real-time, improving crane rates, shortening vessel stays, as well as providing more up to date information for shippers” Mark Hooper, Head of Operations, DP World Southampton
At DP World London Gateway, digital warehouse management is integral to the successful running of our Logistics Park. The retail and e-commerce businesses based there hugely benefit from the stock control technology in our warehouses, as goods can be tracked from receipt from a ship through to customer dispatch via one system.
Long-term Logistics Park tenant MADE.com recently doubled their space at London Gateway thanks to our winning combination of port-centric logistics infrastructure and innovative digital cargo management. It gives the retailers just-in-time supply chain the confidence that what they promise to their customers is what will be delivered.
https://www.youtube.com/watch?v=jcMljPLhSXs
Here at DP World, we’re on a mission to maximise supply chain efficiency through digitalisation, empowering our customers with the information they need to make the right logistics decisions, not to mention reducing costs.
Alongside digital-first cargo management systems, scalable space options and our port-centric infrastructure, we are working to build the next generation of connected cargo transport.
In less than 75 days, DP World will exhibit this bright future at Expo 2020 Dubai. There we’ll showcase how new technologies such as Virgin Hyperloop and Boxbay are set to change freight and port operations as we know it.
I’ll be sure to share insights on this ground-breaking tech after I visit Dubai and our Expo Pavilion, and explain how we can use these new tools to revolutionise British trade.
By combining transparent software with industry-first physical technology, DP World is leading the way.